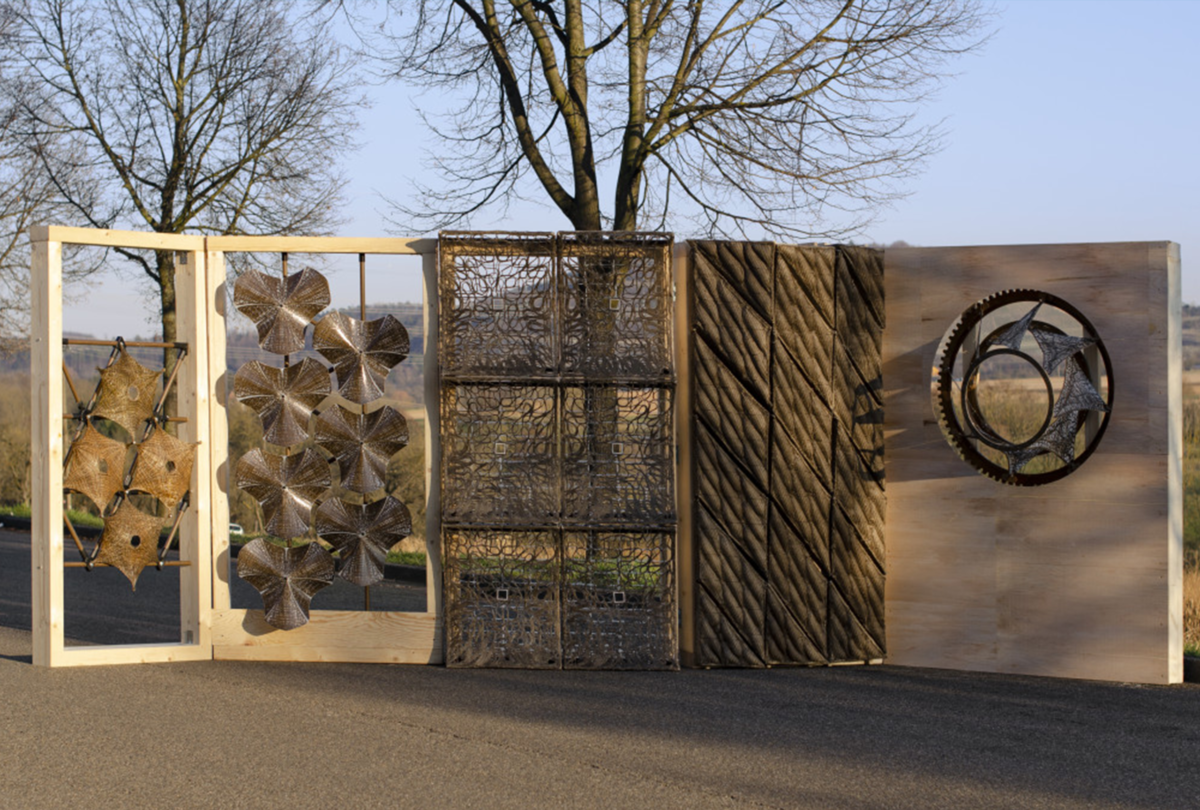
BIO FACADE PANELS
Since resource-intensive materials like steel, concrete, etc. are still predominantly used in the building industry, different emerging technologies and materials have been investigated as their lightweight alternative. One of these are fiber-reinforced polymers (FRP) and their automatic fabrication techniques. BioMat group at University of Stuttgart focuses on natural fibers.
Five different concepts of biocomposite facade panels were developed by using an additive 2D process (so-called Tailored Fibre Placement) where natural fibers were deposited according to design, fabrication method, and required structural performance. The entire process from the design to fabrication was done within one semester. This included: Design of panels and their functional concept, computational designed 2D fiber pattern, design and development of moulding/forming methods with a focus on adaptivity and reusability, binder vacuum-assisted infusion/impregnation, integration of soft or hard actuators, design and development of supporting structure, and robotic assembly. Each concept was presented on a frame with various widths (100-140cm) and a height of 220 cm.
Shading panels
Six panels were computationally designed based on solar radiation which defined fiber patterns and shapes. Panels get into the final shape by stretching a front surface over a frame from balsa and flax fibers. The final pattern was adapted to a customized gripper installed on a cooperative robotic arm which was used to assemble on supporting structure. Each panel covers ca 0,43 m2 and weighs around 2kg.
Sandwich panels
These panels were focused on acoustic absorption and adaptive moulding. Panels from flax fibers and non-woven flax fabric integrated air tubes which were inflated and constrained by tailored fiber patterns which gave to panels a folded-like structure. Each panel had ca 0,27 m2 and a weight of ca. 2 kg. All eighteen panels used an adaptive curing frame allowing fabrication of different shapes. A special gripper was developed for assembly by a cooperative robot.
Adaptive panels
This concept integrated shape memory alloy (Nitinol) as a compliant actuator for opening and closing shading panels. Into each biocomposite panel, flexible hinges were tailored allowing a folding similar to an umbrella. Panels were controlled via smartphone and light sensors Panels were carried by biocomposite pultruded profiles. Each panel weighs only 0,2 kg and covers a size of 0,19m2.
Chitosan panels
These panels experimentally applied chitosan as a more ecological alternative to resin binders for Biocomposites. Flax fibers were tailored on a jute textile their pattern was computationally generated based on principle stress lines. Chitosan is a polysaccharide made by treating the chitin shells of shrimp and other crustaceans. Each panel had a hexagonal shape with a radius of 25 cm and a weight of ca. 0,1 kg.
Rotating panel
It is a shading element that by rotation optimizes sunrays in the interior. The entire system consisted of eight lightweight biocomposite fins combining flax fibers with glass fiber textile. Each fin inspired by the dragonfly wing weighs only around 50 g. Together with the entire gear system, the element (1,2 m in diameter) weight is around 7 kg.
Realization: 10/2021– 02/2022
Department: BioMat at ITKE, Uni Stuttgart
Supervisor: Jun.-Prof. Dr.-Ing. Arch. Hanaa Dahy
Tutors: Dr. Jan Petrš with great support from Benjamin Grisin, Paulina Grabowska, Evgenia Spyridonos, and Asmaa Hasan
Students WS21 (Design studio: Digital Design and Fabrication of Biocomposite Facade Panels):
Siegrid Daniela Viersbach Gordillo, Julian Schwarzenbacher, Mai Thi Nguyen, Ginster Bauer, Amay Shah, Hanna Labanava, Shuangying Xu, Petrit Isai, Niklas Dietrich, Daniel Pauli, Jonas Gorges, Kristian Fisinski, Alina Boss, Anton Kussinna, Erlin Gjolla, Florian Rebmann, Leonard Rieck, Ela Kmita, Vanessa Erb, Johanna Abheiden
Students Scientific Assistant: Matay Kaplan
Cooperation (Composites): Institute of Aircraft Design, Uni. Stuttgart – Prof. Dr.-Ing. Peter Middendorf, Dr. Stefan Carosella, Dipl.-Ing. Benjamin Grisin
Cooperation (Chitosan): Institute of Interfacial Process Engineering and Plasma Technology, Uni. Stuttgart – Dr. Linus Stegbauer, Dr. Amrita Rath
Cooperation (Quality control): Institute of Engineering Geodesy, Uni. Stuttgart – Prof. Dr. Ing. Volker Schwieger, M. Sc. Laura Balange, Dipl.-Ing. Lyudmila Gorokhova
Cooperation (Acoustics): Institute for Acoustics and Building Physics, Uni. Stuttgart -Prof. Dr.-Ing. Philip Leistner, Dipl.-Ing. Eva Veres
Cooperation (Facades): Schüco, Prof. Daniel Arztmann
Tech. Support: M. Sc. Sergej Klassen, M. Sc. Kai Stiefenhofer, M. Eng. Aleksa Arsic
Photos: Masih Imani
Financial support: EXC 2120: Cluster of Excellence IntCDC project by German Research Foundation (DFG) within RP(06).